Push Back Rack
If you’re short on space, a push back rack may be the right solution for you. These offer high storage density. Pallets are pushed back by subsequent pallet loading, while exposing the next car. Much like the products in a vending machine work, when removing a product from a push back rack, the forklift will take out the front pallet, allowing the pallet on the carts behind it to gently roll to the front of the rack. (Push back rack consists of nesting carts which move by gravity on steel rails. Each pallet has its own cart.) This makes for easy placement—it allows you to store pallets two to five deep—and retrieval—retains easy access to a variety of different products.
With a push back rack, you’re afforded more space. In fact, push back racks offer up to 90% more product storage than selective rack systems. Retrieval is also easier as you can store products on different levels while providing a large target for loading and unloading. It maximizes space utilization with a last in, first out (LIFO) approach to inventory control. The system is a LIFO system in which forklift operators never enter the rack.
Pushback warehouse systems are used extensively in high density storage facilities providing superior selectivity and cost benefits when compared with other deep warehouse storage alternatives. These warehouse storage racks provide the flexibility to store multiple SKU’s and eliminates aisles previously needed in a selective rack environment. These systems are front loading/unloading, which reduces labor costs when compared to double-deep and drive-in models.
Push Back rack provides all of the density of a drive-in system without having to drive into the rack. This feature helps maintain the pallet rack system and holds damage to a minimum. We can help you install a complete pushback rack and industrial storage systems to meet your requirements include pallet support, special pallets and more.
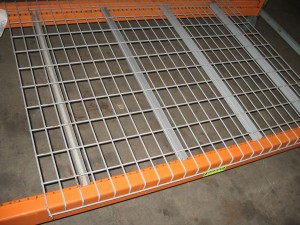